Virtual Reality: Engaging new generations and increasing operator proficiency
- share
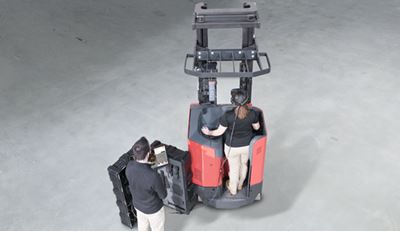
The manufacturing industry plays a key role in our nation’s current and future economic prosperity. However, the labor shortage and skills gap pose some serious challenges to today’s companies. Nearly 3½ million manufacturing jobs will need to be filled in the next decade, but the skills gap is expected to result in two million of those jobs going unfilled.
The manufacturing industry plays a key role in our nation’s current and future economic prosperity. However, the labor shortage and skills gap pose some serious challenges to today’s companies. According to the Manufacturing Institute and Deloitte, nearly 3½ million manufacturing jobs will need to be filled in the next decade, but the skills gap is expected to result in two million of those jobs going unfilled.
As the labor shortage plagues the industry, plant managers are struggling to find new ways to attract talent and drive further innovation within their organizations. To address these challenges, manufacturers are collaborating with technology companies to design virtual reality (VR) simulators that can serve as educational tools to assist in attracting new generations, educating new and existing forklift operators more efficiently, and increasing employee retention rates.
Hands-on engaging education for operators
A virtual-reality instructional tool allows operators to learn on the actual equipment or controls that they will be using on the floor while in a simulated environment. The tool provides advanced, hands-on instruction that is designed to improve operator skills and build confidence. The learning tool lets an instructor work alongside an operator as he or she goes through modules of guided lessons that increase in complexity and build upon principles learned in earlier lessons — providing a consistent experience and reinforcing desired behaviors. Throughout the lessons, the instructor can monitor the operator’s performance and provide real-time feedback.
Potential candidates lacking industry experience can use this progressive coaching tool to learn the skills needed to excel in a warehouse environment. As the operator progresses through the modules, the software uses scenarios that simulate an interference on the warehouse floor to prepare operators for the unexpected. This helps operators familiarize themselves with conditions in the operating environment and work through them in a controlled setting rather than experiencing them for the first time on the actual warehouse floor. Receiving one-on-one coaching through these types of experiences can help prevent product and equipment damage in the long run.
Increased efficiency and productivity
More-engaging and efficient instruction means a more productive warehouse. The goal of instructional VR technology is to optimize throughput by creating more-productive operators. Its data-driven approach can immediately pinpoint an operator’s weak areas, so administrators know whom to target for additional instruction and how. The tool’s software also quickly identifies an employee’s skills and abilities so instruction can be best tailored to individual needs.
These insights and additional instructor feedback can help operators reach higher proficiency levels and make operations run more efficiently. After the operators utilize the VR simulator, the setup and takedown is quick and enhances overall productivity.
Employee value and retention
Although a key benefit of a VR educational tool is to help teach new operators efficiently, it also can be used for existing plant operators. Investing in innovative technology to help further educate existing employees shows that a company sees its employees as valuable assets. Providing the opportunity to learn with innovative workplace tools and recognizing a company’s commitment to its workforce can increase the likelihood that employees will stay in a position long-term.
The need to shrink the labor gap and the inevitable retirement of baby boomers has become a focal point for manufacturing companies. Manufacturing organizations using VR as a learning tool have a unique opportunity to attract new employees, including Millennials and digital-savvy candidates, who may have not otherwise considered this career track. Employers can harness this technology and educate employees in ways they understand and find engaging, which can lead to increased plant efficiencies and stronger employee retention rates.
Submitted by Stacey Patch on Thu, 03/01/2018 - 12:36
Plant Services, Today's Optimized Facility
Read the original post: https://www.plantservices.com/blogs/todays-optimized-facility/virtual-reality-engaging-new-generations-and-increasing-operator-proficiency/